How U.S. Companies Are Responding To Tariff Uncertainty Through Cost Reduction
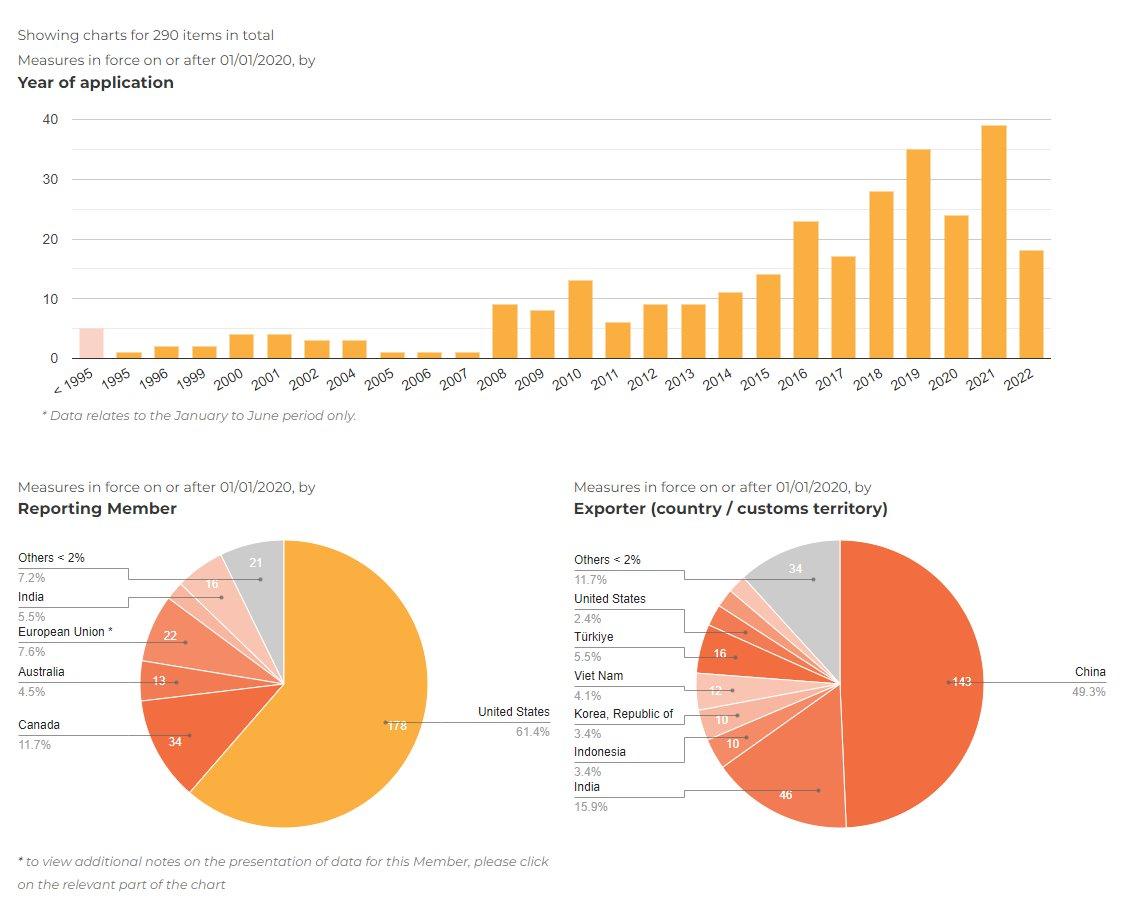
Table of Contents
The unpredictable landscape of global trade, marked by fluctuating tariffs, has significantly impacted U.S. businesses. A recent study showed that 40% of U.S. manufacturers experienced a direct negative impact on their bottom line due to tariffs. This highlights the urgent need for proactive strategies to mitigate these challenges. This article explores how U.S. companies are responding to tariff uncertainty through effective cost reduction. We'll delve into the key strategies businesses are employing to navigate this complex environment and maintain profitability.
<h2>Restructuring Supply Chains to Mitigate Tariff Impacts</h2>
Tariff uncertainty forces companies to rethink their supply chain strategies. A flexible and diversified approach is crucial for minimizing exposure to volatile import costs.
<h3>Sourcing from Alternative Countries</h3>
Diversifying sourcing locations is paramount to reducing reliance on single-source countries. This involves shifting production or sourcing to alternative regions less impacted by tariffs.
- Vietnam: Offers lower labor costs and has benefited from increased foreign investment. However, infrastructure limitations and potential for increased wages need consideration.
- Mexico: Proximity to the U.S. offers advantages in reduced shipping times and costs. The USMCA trade agreement further facilitates trade. However, concerns regarding labor costs and security need evaluation.
- India: A large and diverse manufacturing base, but bureaucratic complexities and infrastructure challenges require careful planning. Stronger intellectual property protection is also a plus.
The process of relocating manufacturing involves significant investment in new facilities, training, logistics management, and establishing quality control processes in new locations. Successfully implementing global sourcing strategies demands meticulous planning and risk assessment.
<h3>Nearshoring and Regionalization</h3>
Nearshoring, the relocation of manufacturing to countries closer to the home market, is another popular strategy. This reduces transportation costs, lead times, and improves supply chain visibility.
- Mexico and Central America: Attractive nearshoring destinations due to geographic proximity and favorable trade agreements. However, wage increases in these regions need to be considered. Some companies are even pursuing reshoring – bringing manufacturing back to the U.S. – although this often comes with higher labor costs.
The shift towards regional supply chains enhances responsiveness to market demands and minimizes disruptions caused by geopolitical events. However, nearshoring may not always offer the same cost advantages as offshoring to countries with significantly lower labor costs.
<h2>Implementing Automation and Technological Advancements</h2>
Technological advancements offer significant opportunities for cost reduction within the manufacturing and supply chain sectors.
<h3>Automation to Reduce Labor Costs</h3>
Automation technologies are rapidly transforming industries, offering significant potential for cost reduction by replacing manual labor.
- Robotics: Robotic process automation (RPA) can streamline repetitive tasks, increasing efficiency and reducing human error.
- Artificial Intelligence (AI): AI-powered systems can optimize production processes, predict maintenance needs, and improve supply chain planning.
While automation investments require upfront capital, the long-term return on investment (ROI) can be substantial. However, companies must carefully assess the potential impact on employment and plan for workforce transitions.
<h3>Utilizing Advanced Analytics for Cost Optimization</h3>
Data analytics is a powerful tool for uncovering areas of waste and inefficiency within the supply chain.
- Predictive Maintenance: AI-powered systems analyze data to predict equipment failures, minimizing downtime and reducing maintenance costs.
- Inventory Optimization: Data-driven insights help companies manage inventory levels more effectively, reducing storage costs and preventing stockouts.
- Route Optimization: Analyzing transportation data improves logistics, reducing fuel consumption and delivery times.
Data-driven decision making allows companies to make informed choices about their operations, leading to significant cost savings and improved efficiency.
<h2>Optimizing Internal Processes for Enhanced Efficiency</h2>
Improving internal processes can yield significant cost reductions without major capital investments.
<h3>Lean Manufacturing Principles</h3>
Lean manufacturing principles focus on eliminating waste and improving efficiency in all aspects of production.
- Waste Reduction: Identifying and eliminating all forms of waste (e.g., overproduction, waiting, transportation, inventory, motion, over-processing, defects).
- Continuous Improvement (Kaizen): Regularly evaluating processes and making incremental improvements to enhance efficiency.
- Six Sigma: A data-driven methodology for process improvement and quality control.
Implementing lean manufacturing principles can drastically reduce production costs and improve overall productivity.
<h3>Streamlining Operations and Reducing Waste</h3>
Streamlining operations focuses on simplifying and optimizing processes to minimize waste and improve efficiency.
- Digital Workflows: Replacing paper-based systems with digital solutions reduces paperwork, improves communication, and minimizes errors.
- Improved Inventory Management: Implementing just-in-time inventory management reduces storage costs and minimizes waste.
- Process Optimization: Regularly reviewing and optimizing all processes to eliminate bottlenecks and improve workflow.
These improvements contribute to a more efficient and cost-effective operation, directly impacting the bottom line.
<h2>Conclusion</h2>
U.S. companies are proactively responding to tariff uncertainty by implementing multifaceted cost reduction strategies. Restructuring supply chains, leveraging automation and advanced analytics, and optimizing internal processes are key elements of this approach. By diversifying sourcing, embracing near-shoring or reshoring, utilizing automation technologies, and implementing data-driven decision-making, businesses can significantly reduce costs and enhance resilience in the face of tariff uncertainty. The key takeaways are that proactive adaptation, a multi-pronged approach, and embracing technology are crucial for success. Start optimizing your supply chain and implementing effective cost reduction strategies today to navigate tariff uncertainty effectively.
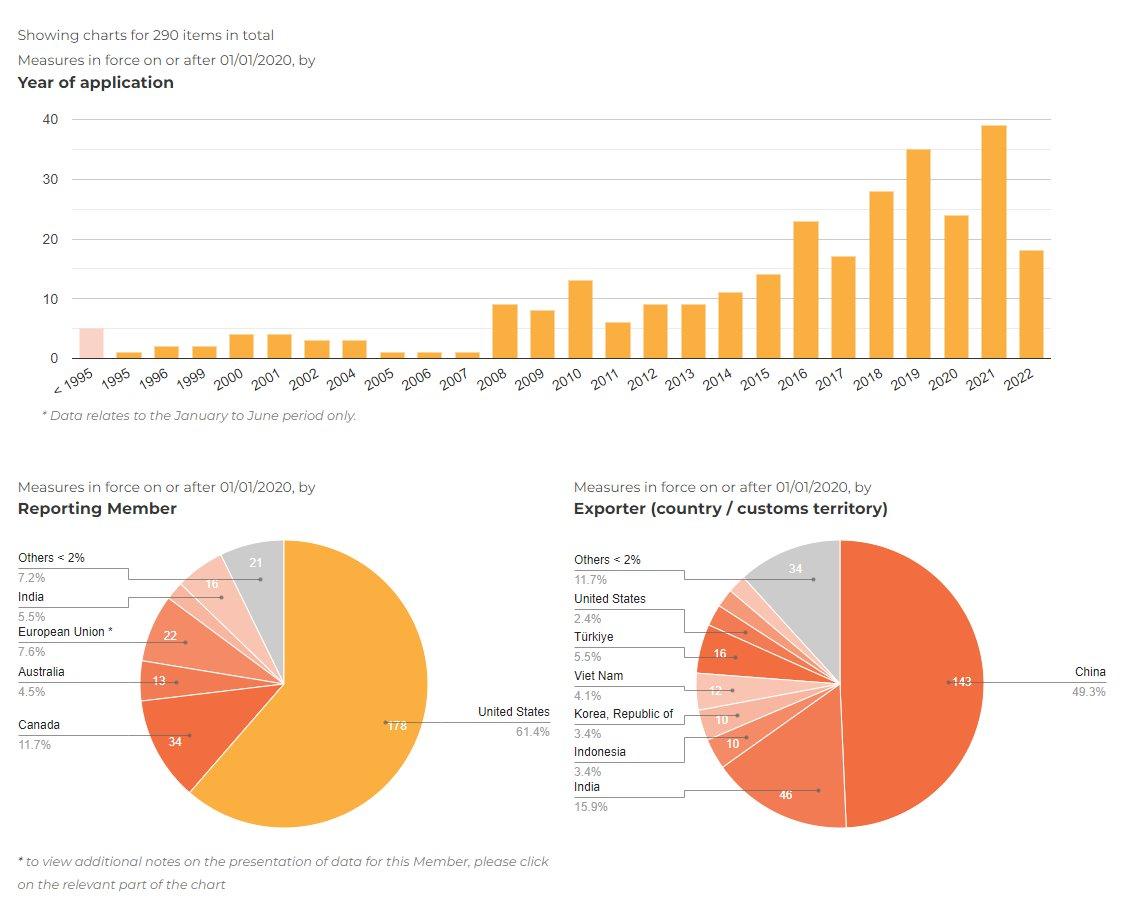
Featured Posts
-
Europe On High Alert Analyzing Recent Russian Military Moves
Apr 29, 2025 -
Analyzing The Countrys Evolving Business Landscape
Apr 29, 2025 -
Wrexhams Rise Ryan Reynolds Reaction To Historic Promotion
Apr 29, 2025 -
Germany Sees Significant Drop In Migration Following Border Control Tightening
Apr 29, 2025 -
Strong Reliance Earnings Positive Outlook For Indian Large Cap Equities
Apr 29, 2025
Latest Posts
-
From Humble Beginnings The Story Of Macario Martinezs Rise To National Prominence
Apr 29, 2025 -
Macario Martinezs Overnight Success A Street Sweepers Journey To Fame
Apr 29, 2025 -
Macario Martinez From Street Sweeper To National Celebrity
Apr 29, 2025 -
Understanding High Stock Market Valuations Bof As Investor Guidance
Apr 29, 2025 -
Ignoring High Stock Valuations Bof As Rationale For Investors
Apr 29, 2025