U.S. Businesses Implement Cost-Cutting Strategies In Response To Tariffs
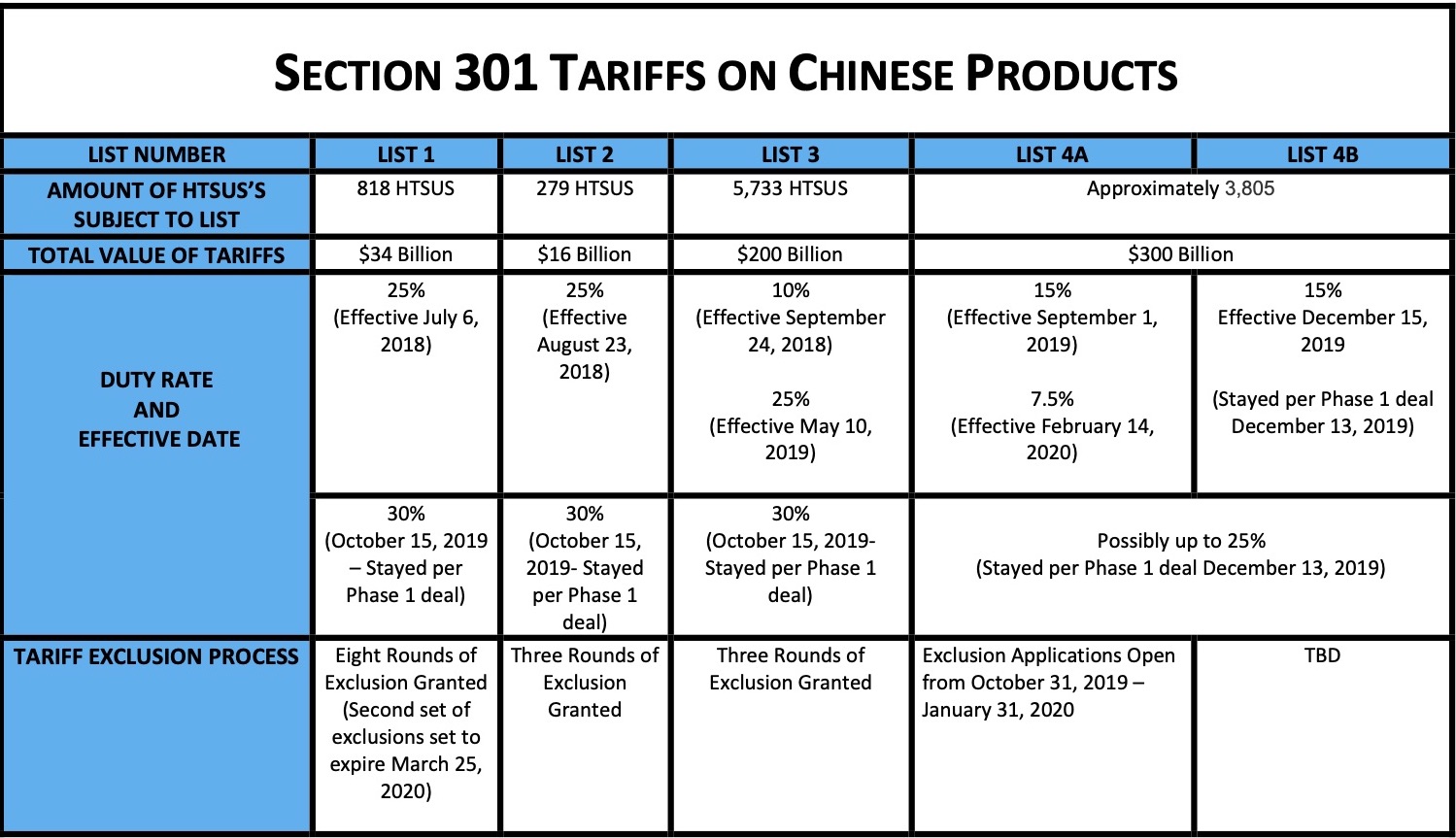
Table of Contents
Restructuring Supply Chains to Minimize Tariff Impacts
The impact of tariffs on imported goods has prompted many U.S. businesses to re-evaluate their global supply chains. Minimizing these costs requires strategic adjustments, focusing on two key areas: nearshoring, reshoring, and diversifying sourcing strategies.
Nearshoring and Reshoring Initiatives:
Businesses are increasingly relocating manufacturing and sourcing operations closer to home to avoid or reduce tariff costs. This involves bringing production back to the U.S. (reshoring) or moving it to nearby countries (nearshoring).
- Examples: Several apparel companies have begun reshoring production from countries like China and Vietnam to reduce reliance on tariff-affected goods. Similarly, some electronics manufacturers are nearshoring production to Mexico to leverage lower labor costs and proximity to the U.S. market.
- Cost-Benefit Analysis: While reshoring and nearshoring may increase labor costs, the savings from avoided tariffs often outweigh these expenses, especially for high-volume products. A thorough cost-benefit analysis considering transportation, labor, and tariff costs is crucial for effective decision-making.
- Challenges: Reshoring presents significant challenges, including higher labor costs compared to many overseas locations and the need for robust domestic infrastructure to support increased production. Finding skilled labor and adapting existing facilities can also be significant hurdles.
Diversifying Sourcing:
Reducing reliance on single-source suppliers in tariff-affected countries is another crucial strategy. Diversifying the sourcing base across multiple countries with favorable trade agreements mitigates risk and reduces vulnerability to tariff fluctuations.
- Benefits: Diversification offers significant advantages, including reduced risk associated with political instability or supply chain disruptions in a single country. It also provides access to a wider range of suppliers, potentially leading to better pricing and quality.
- Risk Mitigation: Implementing robust risk management strategies is essential. This includes thorough due diligence on potential suppliers, contractual agreements protecting against price increases, and establishing backup suppliers to ensure continuity of supply.
- Challenges: Finding reliable alternative suppliers with comparable quality and pricing can be time-consuming and resource-intensive. Effective communication and coordination are critical to managing a diverse supply chain.
Optimizing Internal Operations for Efficiency Gains
Internal operational efficiency plays a crucial role in mitigating the impact of tariffs. Focusing on automation and lean manufacturing principles can significantly reduce costs and improve productivity.
Automation and Technological Advancements:
Implementing automation technologies reduces labor costs and increases overall productivity. This can range from robotics on factory floors to AI-powered software for supply chain management.
- Examples: The use of robotic process automation (RPA) in administrative tasks, automated guided vehicles (AGVs) in warehouses, and AI-powered quality control systems are becoming increasingly common.
- ROI Analysis: A detailed ROI analysis is crucial to justify the investment in automation technologies. Factors like initial investment costs, ongoing maintenance, and labor cost savings must be carefully evaluated.
- Challenges: Implementing automation often requires significant upfront investment, employee retraining, and integration with existing systems.
Lean Manufacturing and Waste Reduction:
Adopting lean manufacturing principles minimizes waste, streamlines operations, and enhances efficiency. This includes eliminating unnecessary steps, reducing inventory, and improving workflow.
- Examples: Implementing Kanban systems for inventory management, Kaizen events for continuous improvement, and 5S methodology for workplace organization are all effective lean techniques.
- Quantifiable Benefits: Lean manufacturing leads to quantifiable benefits, such as reduced lead times, lower inventory costs, and improved quality.
- Challenges: Successfully implementing lean methodologies requires a cultural shift within the organization, commitment from all levels of management, and continuous monitoring and improvement.
Negotiating with Suppliers and Exploring Alternative Materials
Proactive negotiation and material substitution are powerful strategies to reduce costs affected by tariffs.
Renegotiating Contracts:
Companies are actively negotiating with existing suppliers to secure more favorable pricing and payment terms. This requires a strategic approach and a clear understanding of market conditions.
- Strategies: Effective negotiation strategies involve thorough market research, building strong supplier relationships, and presenting a clear case for price adjustments based on tariff impacts.
- Challenges: Renegotiating contracts can be challenging, especially if supplier relationships are already strained. A collaborative approach focused on mutual benefit is often more effective than an adversarial one.
- Impact on Supplier Relationships: Maintaining strong supplier relationships is crucial during this process. Open communication and transparency are key to ensuring a successful outcome.
Substituting Materials:
Exploring and implementing alternative materials or components reduces reliance on tariff-affected products. This requires careful consideration of product quality and cost implications.
- Examples: Switching to domestically sourced materials, using substitute materials with similar properties, or redesigning products to reduce the use of tariff-affected components.
- Impact on Product Quality and Cost: Choosing substitutes requires careful evaluation to ensure they meet quality standards while remaining cost-effective. Thorough testing and validation are essential.
- Challenges: Finding suitable alternatives that meet performance and quality requirements can be difficult. This may necessitate design changes and potentially impact product features.
Conclusion:
U.S. businesses are responding to tariffs by implementing a range of cost-cutting strategies, from restructuring global supply chains to optimizing internal operations and renegotiating supplier contracts. These measures are crucial for maintaining competitiveness in a challenging economic environment. The successful implementation of these strategies requires careful planning, proactive management, and a commitment to continuous improvement. To learn more about effective cost-cutting strategies for mitigating the impact of tariffs on your business, explore resources on supply chain optimization and operational efficiency. Don't let tariffs cripple your profitability—implement effective cost-cutting strategies today!
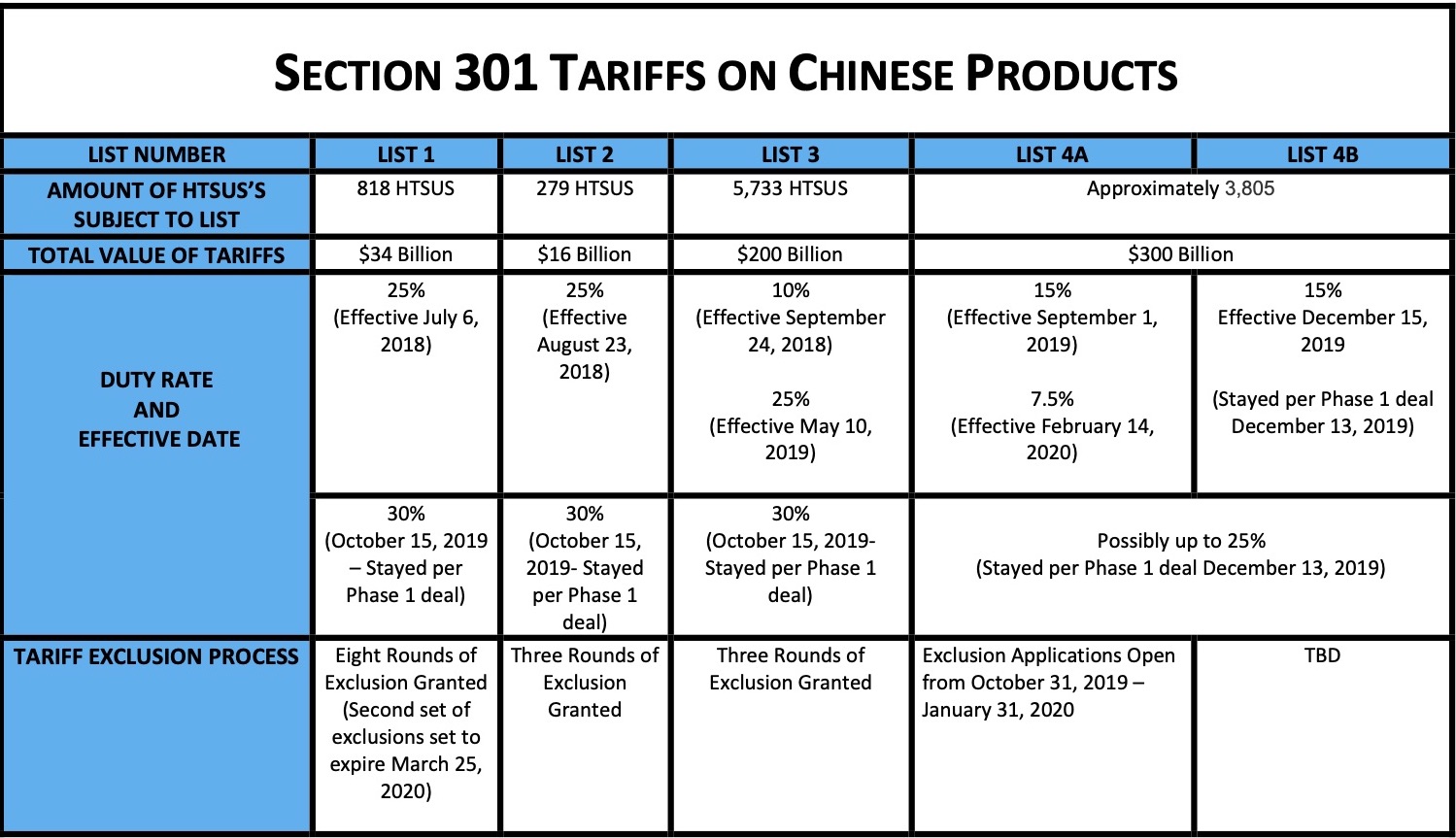
Featured Posts
-
Russias Ukraine Offensive North Korean Troop Deployment Confirmed
Apr 29, 2025 -
160km Mlb
Apr 29, 2025 -
Court Rules In Favor Of Ayesha Howard In Anthony Edwards Paternity Case
Apr 29, 2025 -
U S Companies Slash Costs Amid Tariff Uncertainty
Apr 29, 2025 -
Israel Under Pressure To Reopen Aid Channels To Gaza Strip
Apr 29, 2025
Latest Posts
-
Macario Martinez From Street Sweeper To National Celebrity
Apr 29, 2025 -
Understanding High Stock Market Valuations Bof As Investor Guidance
Apr 29, 2025 -
Ignoring High Stock Valuations Bof As Rationale For Investors
Apr 29, 2025 -
Stock Market Valuations Bof As Reassuring View For Investors
Apr 29, 2025 -
The Countrys Emerging Business Hubs A Geographic Analysis
Apr 29, 2025