Are American Workers Ready For The Return Of Manufacturing Jobs?
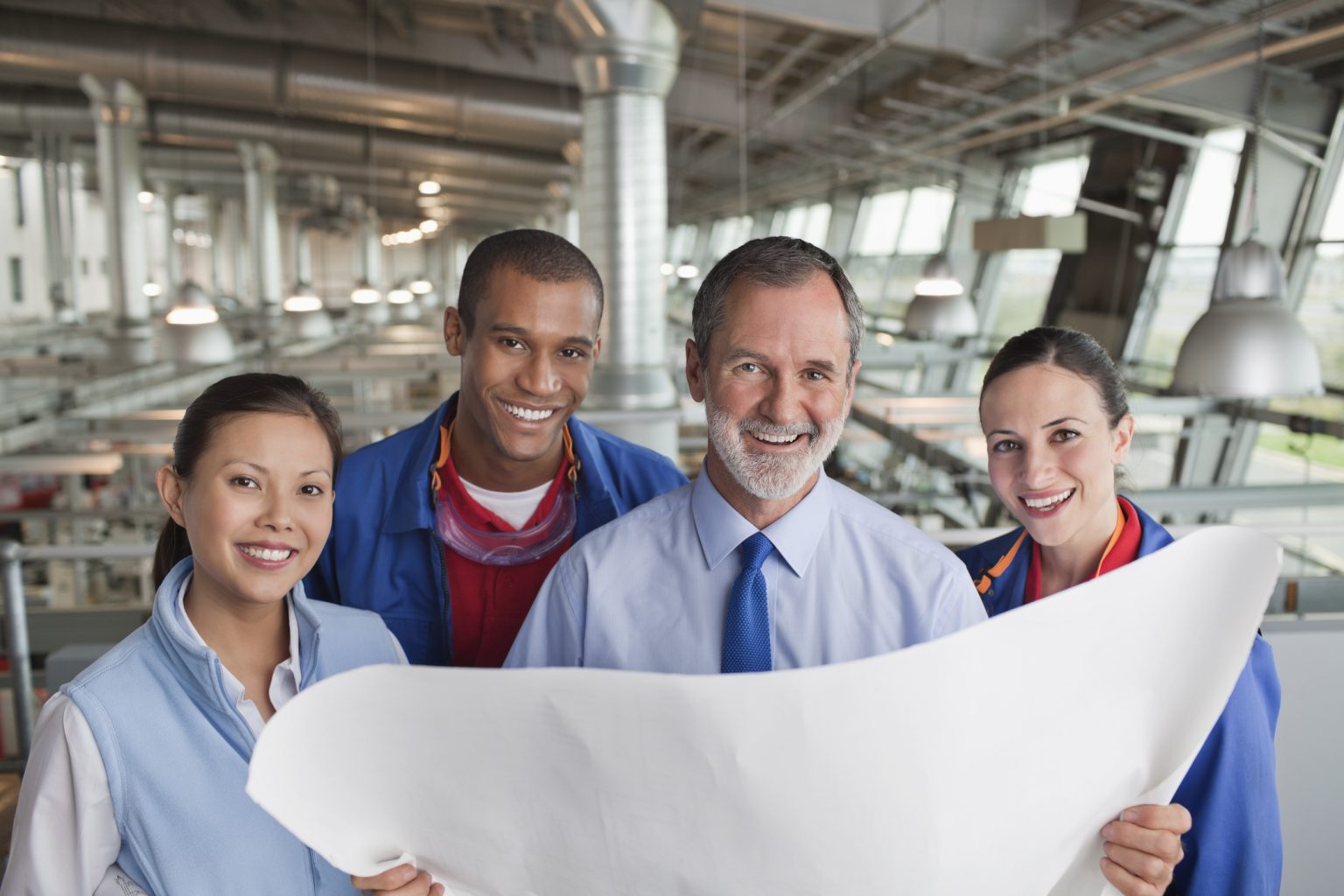
Table of Contents
The Skills Gap: A Major Hurdle for Manufacturing's Revival
The skills gap represents a significant challenge to the revitalization of the US manufacturing sector. A mismatch exists between the skills possessed by the available workforce and the skills demanded by modern manufacturing facilities.
Outdated Skills and the Need for Upskilling/Reskilling Initiatives
- Outdated skills: Many workers possess skills in traditional machining techniques that are no longer sufficient for advanced manufacturing processes.
- Advanced manufacturing skills: The modern manufacturing landscape requires proficiency in robotics, automation systems, programming (especially PLC and CNC programming), data analytics, and sophisticated quality control methodologies.
- Bridging the gap: Government and private sector initiatives are crucial, including apprenticeships, vocational training programs, and online courses focusing on advanced manufacturing technologies. The Manufacturing USA network, for example, plays a vital role in this effort.
Technological advancements have dramatically altered the skill requirements within manufacturing. The rise of Industry 4.0, characterized by smart factories and interconnected systems, necessitates a workforce adept at utilizing and maintaining these sophisticated technologies. Simply possessing manual dexterity is no longer enough; proficiency in technology integration and problem-solving is now paramount.
Attracting and Retaining Talent in Manufacturing
Attracting and retaining a skilled workforce requires a multi-pronged approach:
- Competitive wages and benefits: Manufacturing jobs must offer salaries and benefits packages competitive with other sectors to attract and retain top talent.
- Improved working conditions: Modern manufacturing facilities need to prioritize worker safety, ergonomics, and a positive work environment to counter negative perceptions of the industry.
- Addressing negative perceptions: Marketing campaigns highlighting the rewarding aspects of manufacturing careers, emphasizing technological advancements and career progression opportunities, are necessary to change the public perception of manufacturing jobs.
Targeting younger generations requires innovative recruitment strategies. Highlighting the creative and technological aspects of modern manufacturing, showcasing career paths and opportunities for advancement, and partnering with educational institutions to engage students early are essential steps.
Automation and the Future of Manufacturing Jobs
Automation is rapidly transforming the manufacturing landscape, impacting both job displacement and creation.
The Role of Automation in Modern Manufacturing
- Automated processes: Robotics, artificial intelligence (AI), 3D printing, and advanced sensor technologies are automating various manufacturing processes.
- Job displacement and creation: While some jobs will be displaced by automation, new roles requiring expertise in operating, maintaining, and programming these technologies are being created.
- Automation expertise: The demand for skilled technicians, engineers, and programmers who can design, implement, and maintain automated systems is increasing significantly.
The shift is from predominantly manual labor to skilled technical roles. Workers need to possess the skills to interact with and troubleshoot automated systems, analyze data from sensors and machines, and adapt to constantly evolving technologies.
Adapting the Workforce to Automation Technologies
- Targeted training programs: Investments in training programs specifically focused on automation technologies are essential.
- Industry-education partnerships: Collaboration between educational institutions and manufacturing companies is vital to ensure that training aligns with industry needs.
- Lifelong learning: A culture of continuous learning and upskilling is necessary to ensure that workers can adapt to ongoing technological advancements.
Successful examples of workforce adaptation often involve proactive partnerships between manufacturers and educational institutions, leading to customized training programs and certifications that equip workers with the necessary skills.
Education and Training: Preparing the Next Generation of Manufacturers
Education and training play a critical role in preparing the next generation of manufacturers.
The Importance of STEM Education in Manufacturing
- STEM emphasis: A strong foundation in science, technology, engineering, and mathematics (STEM) is crucial for success in modern manufacturing.
- School-manufacturer partnerships: Partnerships between schools and local manufacturers offer students hands-on experience and exposure to career opportunities.
- Engaging youth: Early exposure to STEM fields and manufacturing careers through outreach programs, internships, and STEM competitions can inspire future generations.
Early exposure to manufacturing careers is particularly vital in inspiring young people to pursue STEM fields. Showcasing the creative and problem-solving aspects of these careers can help counter negative stereotypes.
Community Colleges and Vocational Training Programs
- Specialized training: Community colleges and vocational schools provide crucial specialized training in specific manufacturing skills and technologies.
- Industry certifications: Industry-recognized certifications demonstrate competency and increase employability.
- Local partnerships: Collaborations with local manufacturers ensure that training programs are relevant to industry needs and often lead to job placements.
The success rate of vocational training programs is often high when partnerships with local manufacturers are established, providing graduates with practical experience and direct connections to employment opportunities.
Wage Expectations and Workforce Demographics
Addressing wage concerns and the challenges of an aging workforce are crucial to the success of the manufacturing sector's resurgence.
Addressing Wage Concerns in Manufacturing
- Competitive compensation: Fair and competitive wages and benefits are essential to attract and retain skilled workers.
- Inflation impact: Wage increases must keep pace with inflation to ensure that manufacturing jobs remain attractive.
- Attracting talent: Strategies to attract talent should include comprehensive compensation packages, benefits, and opportunities for professional development.
Fair compensation is not simply about attracting talent; it's about retaining experienced workers and fostering a positive work environment.
The Aging Workforce and Succession Planning
- Aging workforce challenges: A significant portion of the current manufacturing workforce is nearing retirement, creating a potential knowledge gap.
- Succession planning: Proactive succession planning is vital to ensure the transfer of knowledge and skills to younger generations.
- Knowledge transfer: Mentorship programs, apprenticeships, and comprehensive training programs are crucial for transferring institutional knowledge.
Mentorship programs allow experienced workers to share their knowledge and skills with younger colleagues, ensuring continuity and preserving valuable expertise within the industry.
Conclusion: Are American Workers Ready – and What's Next?
The readiness of the American workforce for the return of manufacturing jobs is a mixed bag. While there's a resurgence in the sector and a desire for American-made goods, significant challenges remain. Addressing the skills gap through upskilling and reskilling initiatives, embracing automation through targeted training, and investing heavily in STEM education and vocational training are crucial for success. The aging workforce necessitates robust succession planning and knowledge transfer strategies. Competitive wages and improved working conditions are paramount in attracting and retaining talent.
Investing in the workforce is crucial for the continued success of the return of manufacturing jobs. Learn more about the reskilling opportunities available and support initiatives that prepare American workers for the future of manufacturing. Let's ensure that American workers are not just ready, but thriving, in this revitalized sector.
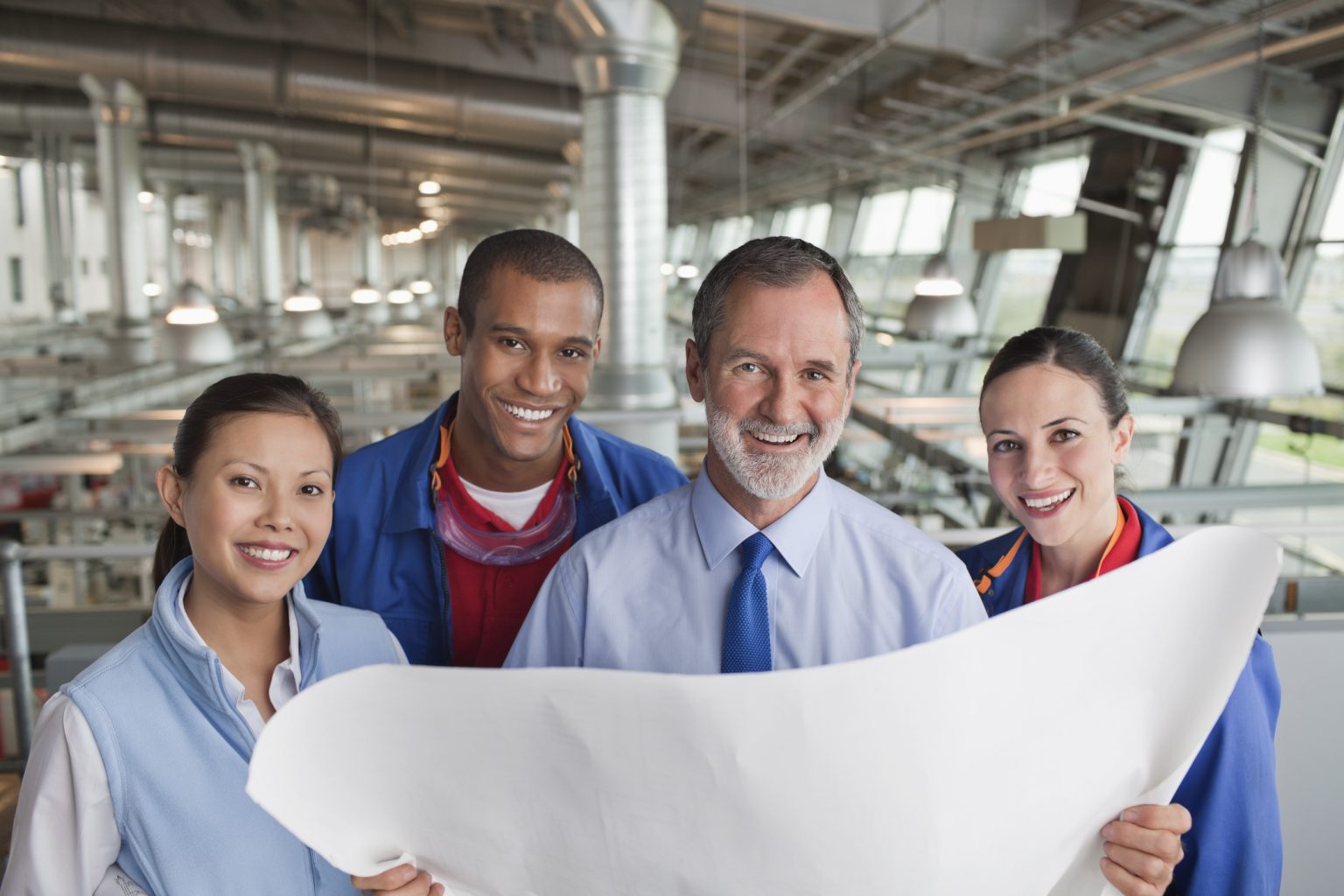
Featured Posts
-
Tampoy Mia Deyteri Eykairia Gia Ton Gamo Tis Marthas
May 20, 2025 -
New Music Monday 2 24 25 Lightning 100s Best New Tracks
May 20, 2025 -
Climate Risk And Your Home Loan How Rising Temperatures Impact Credit Scores
May 20, 2025 -
Us Army Missile Launcher Test In Australia A Geopolitical Analysis
May 20, 2025 -
Cours D Ecriture Inspires D Agatha Christie Par Ia Revolution Ou Imitation
May 20, 2025
Latest Posts
-
Market Reaction Deciphering The Friday Rise In D Wave Quantum Qbts Stock
May 20, 2025 -
Understanding D Wave Quantums Qbts Thursday Stock Price Decrease
May 20, 2025 -
Big Bear Ai Bbai Analyzing The Significant Stock Decline And Implications
May 20, 2025 -
Big Bear Ai Holdings Bbai Evaluating Its Potential As An Ai Penny Stock
May 20, 2025 -
D Wave Quantum Qbts Stocks Friday Rally A Detailed Look
May 20, 2025