The Reality Of All-American Manufacturing: A Tough Business
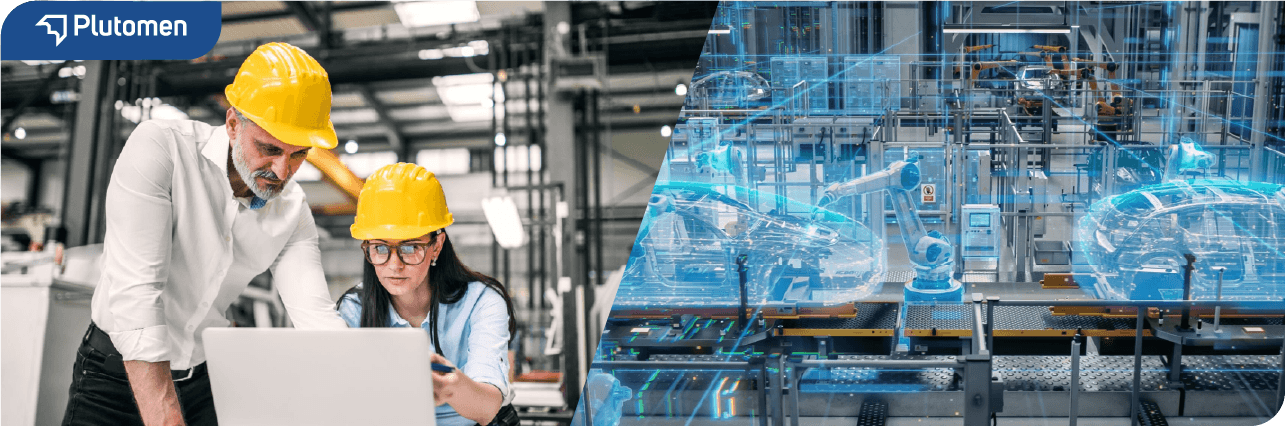
Table of Contents
H2: High Labor Costs and Competition from Overseas
The high cost of labor in the United States presents a significant challenge to All-American manufacturing. This disparity directly impacts profitability, making it difficult to compete with manufacturers in countries with lower wages.
H3: The Wage Gap
The wage gap between the US and other manufacturing hubs is substantial.
- Average Hourly Wages: The average hourly wage for manufacturing workers in the US significantly exceeds those in countries like China, Vietnam, and Mexico. While precise figures fluctuate, the difference often represents a multiple, making American-made goods considerably more expensive to produce.
- Minimum Wage Laws: The impact of minimum wage laws in the US, while intended to protect workers, adds to the overall labor costs, further widening the gap compared to nations with significantly lower minimum wages or less stringent labor regulations.
- Impact on Profitability: This wage differential directly impacts a company's bottom line. Unless American manufacturers can achieve significantly higher productivity or significantly higher pricing, they struggle to compete on price with their overseas counterparts.
H3: Automation's Double-Edged Sword
Automation offers a potential solution to rising labor costs, but it's a double-edged sword.
- Initial Investment Costs: Implementing automation technologies requires substantial upfront investment in new equipment, software, and training. This can be a significant barrier for smaller manufacturers.
- Long-Term Cost Savings vs. Job Losses: While automation can lead to long-term cost savings through increased efficiency and reduced labor costs, it also results in job displacement. This necessitates retraining programs and a focus on developing new skills for the workforce.
- Skills Gap: The transition to automation exacerbates the existing skills gap. The demand for skilled technicians and programmers to maintain and operate automated systems outstrips the supply, hindering the smooth implementation of automation strategies.
H2: Supply Chain Challenges and Material Costs
Maintaining a reliable and cost-effective supply chain is crucial for All-American Manufacturing, but this presents significant challenges.
H3: Raw Material Price Volatility
Fluctuations in raw material prices pose a constant threat to profitability.
- Price Spikes: Recent years have witnessed significant price spikes in materials such as steel, lumber, and various commodities. These unexpected increases drastically impact manufacturing costs and can make it difficult to maintain consistent pricing for finished goods.
- Global Events: Geopolitical instability, wars, and pandemics further disrupt supply chains, leading to material shortages and price volatility. These unpredictable events make long-term planning and cost forecasting extremely difficult.
H3: Logistics and Transportation Bottlenecks
Navigating the complexities of global logistics and transportation presents another significant hurdle.
- Port Congestion: Port congestion, particularly in major US ports, leads to delays in the delivery of raw materials and the shipment of finished goods, increasing costs and impacting delivery timelines.
- Trucking Shortages: A shortage of truck drivers further exacerbates these issues, leading to higher transportation costs and delays.
- Geopolitical Instability: Geopolitical instability and trade disputes can disrupt shipping routes and increase insurance costs, adding to the overall cost of transportation.
H2: Government Regulations and Compliance
Complying with government regulations adds to the cost and complexity of All-American manufacturing.
H3: Environmental Regulations
Environmental regulations are essential but can be costly to implement.
- EPA Regulations: Meeting Environmental Protection Agency (EPA) standards requires significant investment in pollution control equipment and processes. This adds to the overall cost of production and can make it more challenging to compete with manufacturers in countries with less stringent environmental regulations.
- Compliance Costs: The cost of compliance includes not only equipment upgrades but also the expense of ongoing monitoring, reporting, and potential fines for non-compliance.
H3: Bureaucracy and Permitting Processes
Navigating complex bureaucratic processes and obtaining necessary permits can be time-consuming and costly.
- Permitting Delays: Lengthy permitting delays can significantly impact project timelines and increase overall project costs.
- Streamlining Regulations: Streamlining regulatory processes could significantly benefit All-American manufacturing by reducing delays and costs associated with obtaining permits and approvals.
H2: Maintaining a Skilled Workforce
Finding and retaining a skilled workforce is critical for the success of All-American manufacturing.
H3: The Skills Gap in Manufacturing
A significant skills gap exists within various manufacturing sectors.
- Specific Skills Shortages: There's a shortage of skilled workers in areas such as welding, machining, programming, and advanced manufacturing technologies.
- Apprenticeships and Vocational Training: Addressing this skills gap requires a concerted effort to promote apprenticeships, vocational training programs, and STEM education to attract and train the next generation of skilled manufacturing workers.
H3: Attracting and Retaining Talent
Attracting and retaining skilled workers in a competitive labor market requires a comprehensive strategy.
- Competitive Wages and Benefits: Offering competitive wages and benefits packages is essential to attract and retain top talent.
- Company Culture and Advancement Opportunities: A positive company culture and opportunities for professional growth and advancement are also critical in attracting and retaining skilled workers in a competitive labor market.
3. Conclusion:
All-American manufacturing faces numerous significant challenges, including high labor costs, volatile supply chains, complex regulations, and a skills gap. These factors contribute to a complex and challenging business environment. Understanding these challenges is paramount. The key takeaways are the critical need to address the wage gap, improve supply chain resilience, streamline regulatory processes, and invest in workforce development to support the long-term viability of All-American manufacturing. Understanding the realities of All-American manufacturing is crucial for supporting its continued growth and ensuring its long-term viability. Let's work together to build a stronger future for All-American manufacturing, ensuring its continued competitiveness on the global stage.
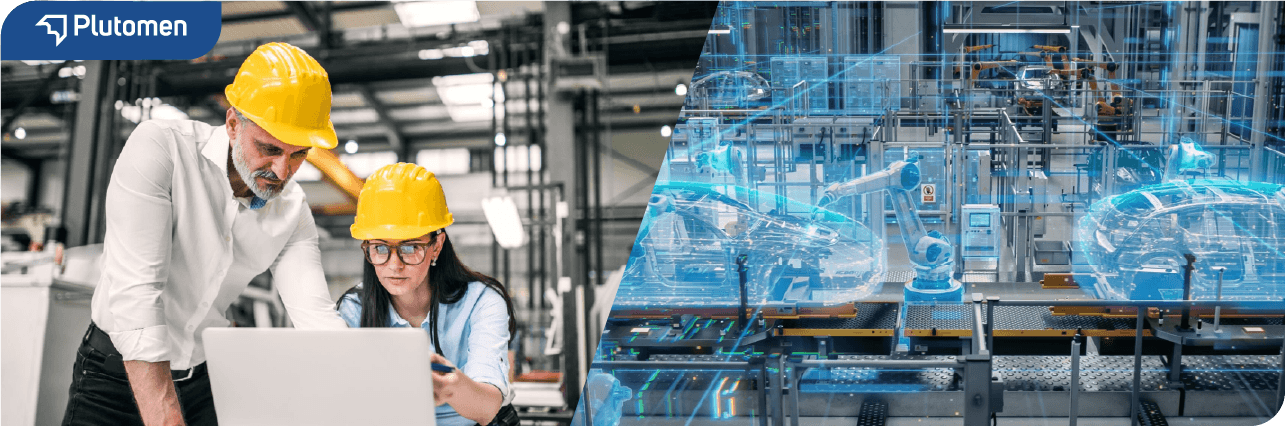
Featured Posts
-
D C Black Hawk Crash Pilots Disregard For Safety Protocol
Apr 29, 2025 -
The D C Black Hawk Crash Examining Pilot Training And Decision Making
Apr 29, 2025 -
Videos Show Raid On Underground Nightclub Over 100 Immigrants Detained
Apr 29, 2025 -
Nyt Strands February 27 2025 Complete Walkthrough And Answers
Apr 29, 2025 -
Ukraine War North Koreas Admission Of Troop Deployment To Russia
Apr 29, 2025
Latest Posts
-
Tremor 2 Netflix Series Kevin Bacons Potential Return Explored
Apr 29, 2025 -
A Tremors Series For Netflix What We Know So Far
Apr 29, 2025 -
Is Tremors Returning To Netflix Updates And Rumors
Apr 29, 2025 -
Tremor 2 Will Kevin Bacon Return In The New Netflix Series
Apr 29, 2025 -
Netflix Tremors Series Release Date Cast And Plot Speculation
Apr 29, 2025