Improving The Accuracy Of Automated Visual Inspection For Lyophilized Vials
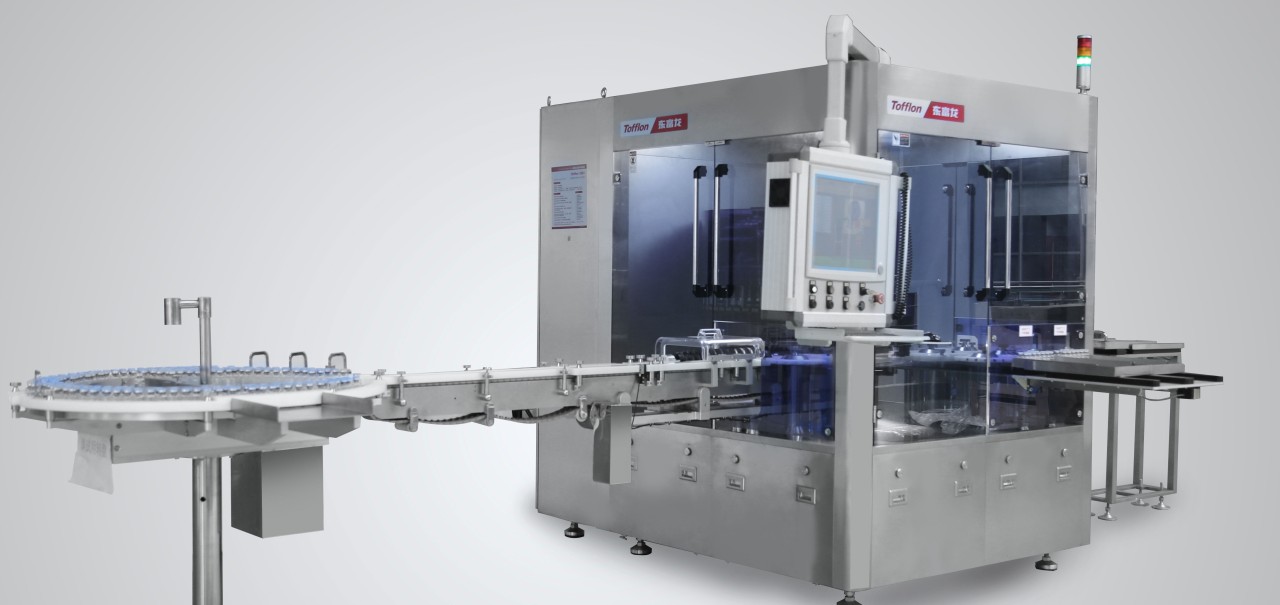
Table of Contents
Challenges in Manual Visual Inspection of Lyophilized Vials
Human visual inspection of lyophilized vials presents several inherent limitations, directly impacting accuracy and consistency. These limitations translate to significant financial and reputational risks for pharmaceutical companies.
- Subjectivity and Inter-operator Variability: Different inspectors may have varying interpretations of what constitutes a defect, leading to inconsistent results. This subjectivity introduces significant variability into the quality control process.
- Fatigue and Reduced Accuracy Over Time: Maintaining focus and accuracy during prolonged periods of manual inspection is challenging. Fatigue inevitably leads to decreased detection rates for subtle defects.
- High Labor Costs and Time Constraints: Manual inspection is expensive, requiring a large workforce and significant time investment. This impacts overall production efficiency and profitability.
- Difficulty in Detecting Subtle Defects: Human eyesight has limitations, especially when identifying minute cracks, particulate matter, or inconsistencies in fill levels within lyophilized vials. These subtle defects can easily be missed during manual inspection.
The consequences of inaccurate inspection are severe. Missed defects can lead to:
- Product Recalls: Recall costs are substantial, impacting profitability and damaging brand reputation.
- Financial Losses: Waste due to defective products adds to production costs.
- Damage to Reputation: Compromised product quality erodes consumer trust and impacts long-term market position.
Advanced Imaging Techniques for Automated Visual Inspection
Automated visual inspection systems leverage advanced imaging technologies to overcome the limitations of manual inspection and achieve significantly higher accuracy. These technologies allow for the detection of even the most subtle defects.
- High-Resolution Cameras and Lighting Systems: High-resolution cameras with specialized lighting configurations (e.g., coaxial, diffused) capture detailed images of each vial, ensuring clear visualization of potential defects.
- Computer Vision Algorithms and Machine Learning: Sophisticated algorithms analyze images to identify and classify defects based on pre-defined criteria. Machine learning capabilities enable continuous improvement in defect detection accuracy over time.
- Spectral Imaging Techniques (e.g., Hyperspectral Imaging): These techniques capture information across a wide range of wavelengths, providing a more comprehensive analysis of vial contents and identifying defects invisible to the naked eye. This is particularly useful for detecting subtle variations in fill level or the presence of specific contaminants.
- 3D Imaging for Complete Vial Analysis: 3D imaging allows for a complete analysis of the vial's geometry, identifying defects such as cracks or irregularities in the vial's shape that might be missed by 2D imaging.
These advanced technologies dramatically improve defect detection capabilities, ensuring higher accuracy in identifying:
- Cracks in the vial walls
- Particulate matter within the lyophilized product
- Inconsistencies in fill levels
- Color variations indicating potential degradation
Optimizing the Automated Visual Inspection System
Optimizing an automated visual inspection system for lyophilized vials is crucial for achieving consistently high accuracy. Several key factors contribute to overall system performance.
- Calibration and Validation: Regular calibration ensures the accuracy of the system's measurements, while validation verifies that the system meets predefined performance criteria.
- Image Processing Algorithms and their Optimization: The selection and optimization of image processing algorithms directly impacts the sensitivity and specificity of defect detection. Continuous refinement of these algorithms is crucial for maintaining optimal performance.
- Data Analysis and Interpretation Techniques: Effective data analysis methods are essential for interpreting the results accurately and identifying patterns in defects.
- Integration with Other Quality Control Systems (e.g., Track and Trace): Seamless integration with other quality control systems improves overall traceability and allows for comprehensive data management.
Regular maintenance and quality control checks are essential for maintaining the accuracy and reliability of the automated visual inspection system over time. This includes periodic calibration, software updates, and preventative maintenance to minimize downtime and ensure consistent performance.
Data Analytics and Process Improvement in Automated Visual Inspection
The data collected by automated visual inspection systems provides valuable insights into the manufacturing process. Analyzing this data enables proactive improvements and significant cost savings.
- Identify Trends and Patterns in Defects: Analyzing defect data over time can reveal trends and patterns, pinpointing specific areas in the manufacturing process that contribute to recurring defects.
- Improve Manufacturing Processes: Identifying root causes of defects allows for targeted process improvements, reducing defect rates and improving overall product quality.
- Reduce Error Rates Over Time: The continuous learning capabilities of machine learning algorithms lead to a reduction in error rates over time, increasing the efficiency and accuracy of the inspection process.
- Predict Potential Issues Before They Arise: By identifying patterns and trends, data analytics can predict potential problems before they occur, allowing for preventative measures to be implemented.
Using data analytics for continuous improvement ensures that the automated visual inspection system remains optimized for maximum accuracy and efficiency.
Implementing Quality by Design (QbD) principles
Implementing Quality by Design (QbD) principles is crucial for ensuring consistent accuracy in automated visual inspection. QbD emphasizes a scientific and risk-based approach to design, development, and manufacturing.
- QbD principles guide the selection of appropriate imaging technologies, algorithm design, and system parameters, ensuring the system effectively addresses the critical quality attributes of the lyophilized vials.
- Design of Experiments (DoE) allows for systematic optimization of system parameters, ensuring the system is robust and performs consistently under various operating conditions.
Ensuring High Accuracy in Automated Visual Inspection for Lyophilized Vials
Automated visual inspection systems offer significant advantages over manual inspection for lyophilized vials, resulting in substantial improvements in accuracy, efficiency, and cost-effectiveness. By leveraging advanced imaging technologies, sophisticated algorithms, and data analytics, these systems provide a robust solution for ensuring high-quality product. The continuous optimization and data-driven improvements contribute to long-term reliability and efficiency. Invest in cutting-edge automated visual inspection technology today to ensure the highest accuracy and efficiency in your lyophilized vial production process.
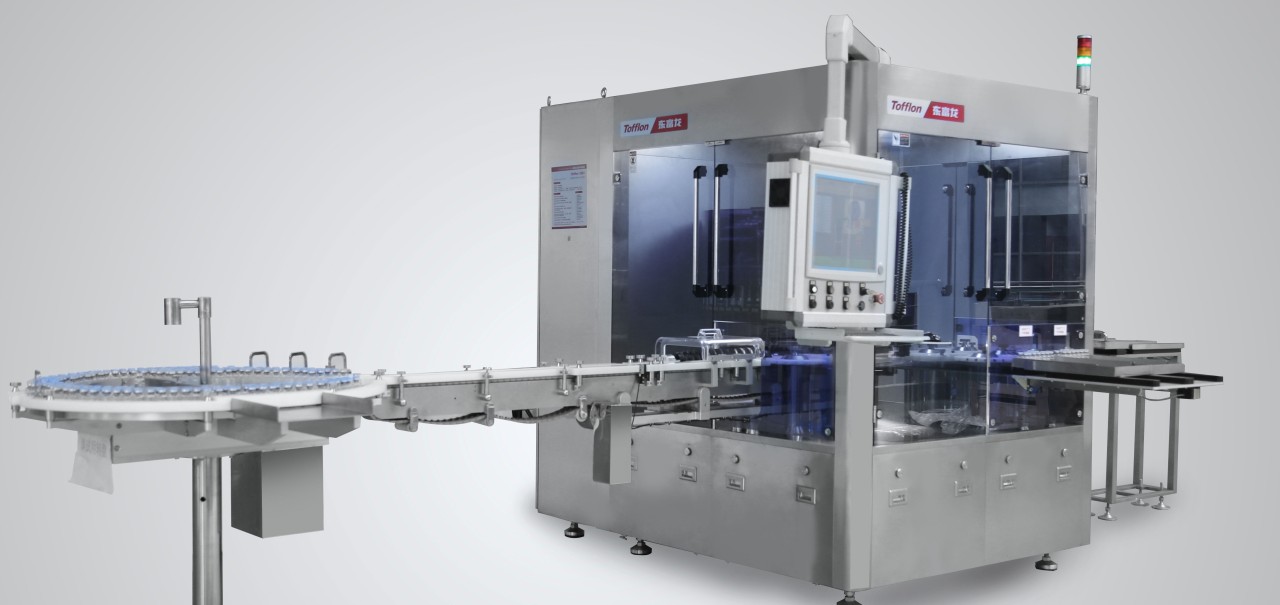
Featured Posts
-
Gpb Capital Founder Sentenced 7 Years For Ponzi Like Scheme
May 11, 2025 -
Confirmed Crazy Rich Asians Series Adaptation With Director Jon M Chu
May 11, 2025 -
Payton Pritchard From Celtic Role Player To Sixth Man Of The Year
May 11, 2025 -
Is Payton Pritchard The Nbas Best Sixth Man Celtics Star Contender
May 11, 2025 -
Fun Takes Flight Making Air Travel Enjoyable And Affordable
May 11, 2025