Automated Visual Inspection Of Lyophilized Vials: Challenges And Solutions
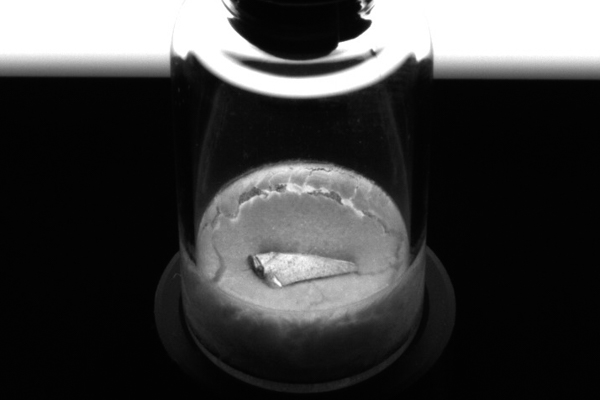
Table of Contents
Challenges in Automated Visual Inspection of Lyophilized Vials
Implementing automated visual inspection for lyophilized vials presents several unique challenges. The inherent variability of the lyophilized product, complexities in image acquisition, and the need for high throughput all contribute to the complexity.
Variability in Lyophilized Product Appearance
Lyophilized cakes exhibit considerable natural variability in color, texture, and shape. This variability makes it difficult to differentiate between acceptable variations and actual defects, leading to both false positives and false negatives. This significantly impacts the accuracy and efficiency of the inspection process.
- Examples of challenging variations: Slight color variations due to differences in the freeze-drying process, variations in cake morphology (e.g., slightly irregular shapes), and the presence of minor surface irregularities.
- Impact on throughput and accuracy: False positives lead to increased rejection rates and reduced throughput. Conversely, false negatives can lead to the release of substandard products, posing significant safety risks. Robust algorithms are needed to address these challenges.
Lighting and Image Acquisition Challenges
The translucent nature of vials and the lyophilized product itself creates significant difficulties in obtaining high-quality, consistent images. Shadows and glare often obscure defects, hindering accurate detection. Sophisticated lighting techniques are essential to overcome these hurdles.
- Different lighting techniques and their advantages/disadvantages:
- Structured lighting: Projects patterns onto the vial to enhance surface detail, but can be complex to implement.
- Polarized light: Reduces glare and enhances contrast, but may not be effective for all types of defects.
- Coaxial lighting: Illuminates the vial from the same direction as the camera, minimizing shadows. However, it might not provide enough contrast for subtle defects.
- Impact of vial material on image quality: The type of glass or plastic used in the vial can affect light transmission and reflection, further complicating image acquisition.
High Throughput Requirements
Pharmaceutical production demands high-speed inspection systems to meet the throughput requirements of modern manufacturing lines. Balancing speed and accuracy is a major challenge. Robust hardware and software are essential to ensure reliable and efficient operation.
- Typical throughput requirements: Hundreds or even thousands of vials per hour are typical in high-volume pharmaceutical manufacturing.
- Limitations of current technologies: Some existing systems struggle to maintain accuracy at very high speeds.
- Future technological advancements: Developments in high-speed cameras, advanced image processing algorithms, and parallel processing techniques are crucial to meeting future throughput demands.
Solutions for Effective Automated Visual Inspection
Addressing the challenges outlined above requires a multi-pronged approach, leveraging advanced technologies and innovative techniques.
Advanced Image Processing Techniques
Advanced algorithms are critical for enhancing the accuracy of defect detection. Machine learning and deep learning, in particular, offer significant advantages in analyzing complex images and identifying subtle defects that might be missed by traditional methods. Computer vision plays a vital role in automating the analysis process.
- Specific algorithms used: Convolutional Neural Networks (CNNs) are particularly well-suited for image analysis tasks. Support Vector Machines (SVMs) and other machine learning algorithms can also be employed.
- Advantages of each technique: Deep learning models, such as CNNs, can automatically learn features from large datasets, reducing the need for manual feature engineering.
- Data requirements for algorithm training: Large and representative datasets of both defect-free and defective vials are required to train effective algorithms. Careful data curation and annotation are critical.
Optimized Lighting and Imaging Systems
Minimizing shadows and glare is crucial for accurate image acquisition. Specialized lighting systems, high-resolution cameras, and appropriate image sensors are essential components of a robust automated visual inspection system. Multispectral imaging can provide additional information to enhance defect detection.
- Examples of advanced imaging systems: Systems incorporating multiple light sources, high-dynamic-range (HDR) cameras, and advanced image sensors.
- Their capabilities and limitations: While advanced imaging systems significantly improve image quality, careful consideration must be given to their cost and complexity.
Integration with Existing Production Lines
Seamless integration with existing production lines and data management systems is critical for efficient operation. User-friendly interfaces and efficient data analysis tools are necessary for effective monitoring and control. Regulatory compliance (e.g., 21 CFR Part 11) must also be ensured.
- Integration challenges: Ensuring compatibility with existing equipment, data formats, and software systems.
- Solutions for data management: Implementing robust database systems and secure data transfer protocols.
- Regulatory considerations (e.g., 21 CFR Part 11): Meeting regulatory requirements for data integrity, audit trails, and electronic signatures.
Conclusion
Automated visual inspection of lyophilized vials presents unique challenges due to product variability, imaging complexities, and high throughput requirements. However, advanced image processing techniques, optimized lighting and imaging systems, and seamless system integration offer effective solutions to overcome these hurdles. Employing these technologies is crucial for ensuring the quality and safety of lyophilized pharmaceuticals. By utilizing machine learning, advanced lighting, and efficient system design, manufacturers can significantly improve the accuracy and speed of their inspection processes. Optimize your lyophilized vial inspection process by investing in efficient automated visual inspection systems. Improve your automated visual inspection processes today. Contact leading vendors to learn more about implementing these advanced technologies and revolutionize your pharmaceutical manufacturing.
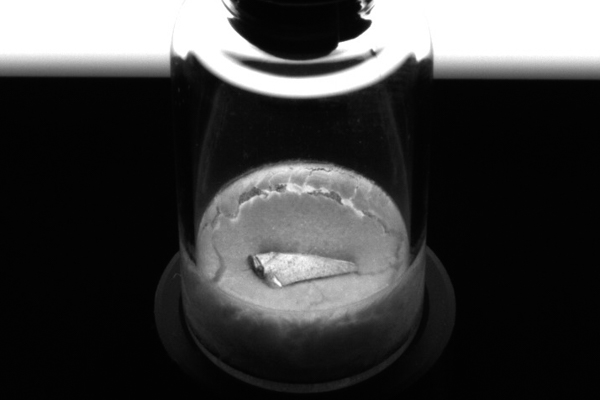
Featured Posts
-
Werder Bremens Victory Over Holstein Kiel Match Report And Analysis
May 11, 2025 -
Nba Award Boston Celtics Guard Declines Campaign
May 11, 2025 -
Unseen Picture Conor Mc Gregor Pays Tribute To Adam Sandler And Happy Gilmore
May 11, 2025 -
The Elusive John Wick Appearances Across Four Films
May 11, 2025 -
Chto Delali Boris Dzhonson I Ego Zhena Vo Vremya Poezdki V Tekhas Foto
May 11, 2025