Addressing Challenges In Automated Visual Inspection Of Lyophilized Vials
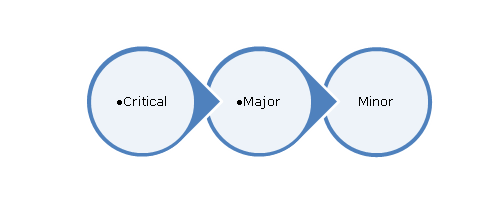
Table of Contents
Challenges Related to Lyophilized Product Characteristics
The inherent variability in lyophilized products significantly impacts the effectiveness of automated visual inspection. Two key challenges stand out: variations in cake appearance and issues related to transparency and refractive index.
Variability in Lyophilized Cake Appearance
Lyophilization processes, while aiming for consistency, often result in variations in the appearance of the lyophilized cake. These variations can range from subtle differences to significant defects, making consistent automated detection extremely difficult.
- Variations in sublimation rates: Uneven sublimation during the freeze-drying process leads to inconsistent cake morphology, including cracks, fissures, and variations in density. This makes it challenging for algorithms to differentiate between acceptable variations and critical defects.
- Differences in formulation: The specific formulation of the drug product significantly influences the cake's appearance. Different formulations exhibit different tendencies towards cracking, collapse, or uneven surfaces, demanding flexible inspection parameters.
- Current AVI system limitations: Many existing AVI systems struggle to reliably differentiate between acceptable variations in cake morphology and actual defects. This leads to either high false positive rates (rejecting good vials) or high false negative rates (accepting defective vials). Improving the algorithms to account for these natural variations is crucial.
Transparency and Refractive Index Issues
The translucent nature of lyophilized cakes presents another significant hurdle. Light scattering and reflections within the vial can mask subtle defects, making accurate detection challenging.
- Distinguishing internal and external defects: It can be difficult to distinguish between defects on the surface of the cake and internal defects within the lyophilized mass. This requires advanced imaging techniques to penetrate the cake and visualize internal structures.
- Advanced imaging techniques: Overcoming these limitations necessitates the use of advanced imaging techniques such as multispectral imaging, which utilizes different wavelengths of light to enhance contrast and reveal subtle defects that might be invisible under standard white light illumination.
- Calibration challenges: Variations in vial transparency and the refractive index of the lyophilized cake can also affect image acquisition and analysis, requiring careful calibration and adjustment of the AVI system.
Technical Hurdles in Automated Visual Inspection System Implementation
Beyond the product-related challenges, several technical hurdles complicate the implementation of effective automated visual inspection systems for lyophilized vials.
High Throughput Demands
Pharmaceutical production lines demand high-speed inspection, posing a significant challenge for AVI systems. The need for speed often compromises the accuracy and reliability of the inspection process.
- Faster image processing algorithms: Developing faster and more efficient image processing algorithms is paramount to meet the throughput requirements of high-speed production lines.
- Maintaining accuracy at increased speeds: The challenge lies in maintaining the accuracy and sensitivity of defect detection while significantly increasing the inspection speed.
- Integration with high-speed production lines: Seamless integration of the AVI system with existing high-speed automated filling and capping lines is essential for effective implementation.
False Positive and False Negative Rates
Balancing sensitivity (avoiding false negatives – missing defects) and specificity (avoiding false positives – rejecting good vials) is a critical challenge. High false positive rates lead to increased rejection rates and wasted product, while high false negative rates risk releasing defective products.
- Sophisticated image analysis algorithms: Minimizing both false positives and false negatives requires sophisticated image analysis algorithms capable of accurately identifying and classifying defects while accounting for variations in cake appearance.
- Rigorous validation and testing: Thorough validation and testing procedures are crucial to ensure the accuracy and reliability of the AVI system, verifying its ability to consistently meet predefined acceptance criteria.
- Regular system calibration: Regular calibration and maintenance of the AVI system are essential to maintain accuracy and consistency over time.
Solutions and Advancements in Automated Visual Inspection for Lyophilized Vials
Significant advancements in imaging technology and artificial intelligence are offering solutions to the challenges outlined above.
Advanced Imaging Techniques
Moving beyond traditional 2D imaging offers significant improvements in defect detection.
- 3D imaging: Three-dimensional imaging techniques provide better depth perception, enabling the identification of internal defects that might be invisible in 2D images.
- Multispectral imaging: By utilizing multiple wavelengths of light, multispectral imaging enhances contrast and reveals hidden defects obscured by light scattering or reflections.
- Hyperspectral imaging: Hyperspectral imaging offers detailed spectral information for enhanced material characterization, allowing for better differentiation between acceptable variations and critical defects.
AI and Machine Learning Integration
Artificial intelligence (AI) and machine learning (ML) algorithms are transforming the capabilities of AVI systems.
- Improved defect classification and recognition: AI and ML algorithms can be trained on large datasets of inspected vials, learning to recognize and classify various types of defects with greater accuracy than traditional methods.
- Reduced false positive and false negative rates: AI-powered systems can significantly reduce both false positive and false negative rates, improving the overall accuracy and reliability of the inspection process.
- Increased robustness and adaptability: AI and ML provide increased robustness and adaptability to variations in production, allowing the system to adjust to changes in formulation or lyophilization process parameters.
Conclusion
Automated visual inspection of lyophilized vials presents unique challenges due to the inherent variability of lyophilized cakes and the demands of high-throughput manufacturing. However, advancements in imaging technology, coupled with the power of AI and machine learning, are paving the way for more robust and accurate inspection systems. By addressing the challenges outlined above, pharmaceutical companies can significantly improve product quality, reduce waste, and increase the efficiency of their lyophilization processes. Investing in advanced automated visual inspection solutions is crucial for ensuring the safety and efficacy of lyophilized drug products. Explore the latest advancements in automated visual inspection of lyophilized vials and improve your quality control processes today!
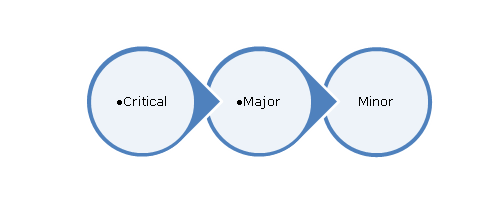
Featured Posts
-
Understanding The Night Hunter Behavior Habitats And Prey
May 11, 2025 -
Aaron Judges 1 000 Game Milestone Hall Of Fame Bound
May 11, 2025 -
Chantal Ladesou Cash Sur Ines Reg Dans Mask Singer Ses Revelations Sur Leur Collaboration
May 11, 2025 -
Is The Mtv Movie And Tv Awards Show Over 2025 Update
May 11, 2025 -
Indy Car Qualifying Palou Triumphs Andretti Drivers Face Challenges
May 11, 2025