A Case Study Addendum: How BYD Became A Leader In EV Battery Manufacturing
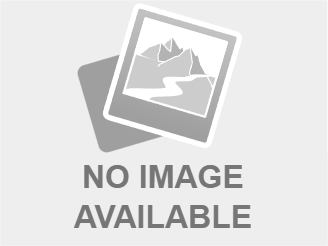
Table of Contents
BYD's Vertical Integration Strategy: A Key to Success
BYD's remarkable rise isn't accidental; it's a testament to a meticulously planned vertical integration strategy. This approach provides unparalleled control over the entire EV battery manufacturing process, from raw material sourcing to the final product.
Control over the Supply Chain
BYD's unique advantage lies in its complete control over the supply chain. Unlike many competitors reliant on external suppliers, BYD manages every stage of production, ensuring consistent quality and minimizing disruptions.
- Raw Material Sourcing: BYD actively invests in securing crucial raw materials like lithium, cobalt, and manganese, reducing dependence on fluctuating market prices and ensuring a stable supply. This includes exploring ethical and sustainable sourcing practices.
- Cell Technology: BYD's innovation in battery cell technology, most notably its Blade Battery, significantly improves energy density, safety, and lifespan compared to traditional cylindrical or prismatic cells.
- Manufacturing Processes: From cell manufacturing to pack assembly, BYD employs state-of-the-art automated systems, leading to increased efficiency and reduced production costs.
The benefits of this vertical integration are multifaceted: reduced costs, enhanced quality control, accelerated innovation cycles, and a significant competitive edge in the BYD EV battery manufacturing sector.
Investment in R&D and Technological Innovation
BYD's commitment to research and development is unwavering. Substantial investments have yielded groundbreaking battery technologies that redefine the possibilities of EV power.
- Blade Battery Technology: This revolutionary technology boasts significantly higher energy density and improved safety features compared to traditional lithium-ion batteries, leading to increased range and performance in EVs. The flat design also maximizes space utilization within the vehicle.
- Lithium Iron Phosphate (LFP) Chemistry: BYD has championed LFP battery chemistry, offering a cost-effective and environmentally friendly alternative to nickel-cobalt-manganese (NCM) batteries. LFP batteries are known for their inherent safety and long lifespan.
- Continuous Innovation: BYD consistently files numerous patents, showcasing its ongoing commitment to pushing the boundaries of battery technology. This ensures they remain at the forefront of innovation in the BYD EV battery manufacturing field.
These innovations directly impact battery performance, enhancing energy density, extending lifespan, and improving overall safety, factors crucial for driving adoption of EVs.
Cost-Effectiveness and Competitive Pricing
BYD's success is not solely attributable to technological superiority; it's also a result of a remarkably cost-effective and competitive pricing strategy.
Economies of Scale and Efficient Manufacturing
BYD's massive production capacity and highly efficient manufacturing processes contribute significantly to lower production costs.
- Gigafactories: BYD operates massive battery production facilities, leveraging economies of scale to drastically reduce per-unit manufacturing costs.
- Automation and Optimization: Advanced automation and continuous process optimization maximize production efficiency, minimizing waste and labor costs.
- Cost Advantage: These combined factors translate into a significant cost advantage over competitors, enabling BYD to offer competitively priced EV batteries.
This cost-effectiveness is a crucial element of their market penetration strategy, making EVs more affordable and accessible to a wider range of consumers.
Strategic Partnerships and Market Expansion
BYD hasn't limited itself to internal growth. Strategic partnerships and aggressive market expansion have solidified its global presence.
- Automotive Partnerships: BYD collaborates with numerous automotive manufacturers globally, supplying them with high-quality EV batteries, boosting both their brand recognition and market reach.
- Global Market Penetration: BYD actively expands into key global markets, establishing a strong presence in various regions, including Europe, Asia, and North America.
- Increased Market Share: These partnerships and market expansions directly contribute to significant market share gains, further solidifying BYD's position as a leader in BYD EV battery manufacturing.
These strategic alliances are instrumental in driving brand recognition, facilitating market penetration, and ultimately accelerating the adoption of EVs globally.
Sustainability and Environmental Responsibility
Beyond economic success, BYD demonstrates a strong commitment to environmental sustainability, a factor increasingly important in the EV industry.
Focus on Sustainable Raw Material Sourcing
BYD actively works to minimize the environmental impact of its operations, focusing on responsible raw material sourcing.
- Ethical Mining Practices: BYD prioritizes sourcing raw materials from mines that adhere to strict environmental and social standards, minimizing negative impacts on ecosystems and communities.
- Recycling Initiatives: BYD actively invests in battery recycling programs, aiming to recover valuable materials and reduce waste. This closed-loop approach is crucial for sustainable battery production.
- Sustainable Supply Chains: BYD actively works with suppliers to establish sustainable and responsible practices across its entire supply chain.
Commitment to Reducing Carbon Footprint
BYD is committed to reducing its carbon footprint throughout its operations.
- Renewable Energy Usage: BYD utilizes renewable energy sources, such as solar and wind power, in its manufacturing processes to reduce reliance on fossil fuels.
- Carbon Offset Programs: BYD actively participates in carbon offsetting programs to further neutralize its environmental impact.
- Efficient Transportation: Optimizing transportation logistics reduces fuel consumption and associated emissions across the entire supply chain.
These sustainable practices enhance BYD's brand image, fostering trust among environmentally conscious consumers.
Conclusion
BYD's dominance in EV battery manufacturing stems from a strategic combination of factors: a vertically integrated approach to control the supply chain, relentless investment in R&D leading to groundbreaking innovations like the Blade Battery, a cost-effective manufacturing strategy enabling competitive pricing, and a strong commitment to sustainability. These elements have propelled BYD to the forefront of the EV revolution.
Explore the future of EV battery technology and learn more about BYD's leadership in this rapidly evolving sector. Understanding the complete case study will reveal how BYD's innovative approaches to BYD EV battery manufacturing are shaping the future of sustainable transportation.
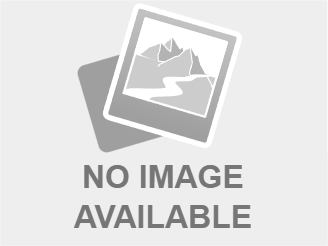
Featured Posts
-
The Gaza Hostage Crisis A Lingering Nightmare For Families
May 13, 2025 -
Is Gambling On Natural Disasters The New Normal The Case Of The La Wildfires
May 13, 2025 -
Ethan Slaters Role In Elsbeth Season 2 Episode 17 Explained
May 13, 2025 -
Analysis Local Reactions To Trumps State Of The Union Address
May 13, 2025 -
The Gaza Hostage Crisis A Continuing Nightmare For Families
May 13, 2025